Bending of sheet metal
The company Production Complex "Svet Shakhtyora" LLC offers sheet metal bending services. Bending of parts is carried out on the German TRUMABEND 850S and V130 equipment (length up to 3000 mm, thickness up to 6.0-12 mm.), which allows you to accurately and quickly give the workpiece the required shape, according to KD.
Bending is a technology of cold plastic deformation of metal. It consists in changing the shape of a metal sheet by deformation using a matrix and a movable punch. Bending makes it possible to make complex three-dimensional metal products.
Free cold (V-shaped) machining of the workpiece is the most popular and widespread variant of metal bending. It is usually performed with a universal or special machining tool on a hydraulic CNC press brake. The die is usually placed in the lower stationary part of the press, and the punch is fixed on the movable working beam of the machine. Thus, the movable punch exerts the necessary pressure on the processed sheet of material and, together with the fixed matrix, it produces the given bends. In other words, the upper part of the workpiece is compressed under the action of the punch and matrix, and the lower part is pressed against the walls of the matrix mechanism and stretched, thus providing the necessary angle and radius of bending. During bending (plastic deformation) of the workpiece, the punch is placed in the inner part of the bending corner, and the matrix is placed on the outside of the bending corner.
The free cold V-form process is generally used for metal blanks between 0.1 and 8 mm thick, but the exact range of possible thicknesses for a particular product depends on the type and grade of metal. It is also necessary to specify the possible bending radii in advance.
Available bending angles for the bending equipment we use are from 24-25 0 up to 170–179 0 It is also possible to achieve smaller bending angles. For this, the matrix of the hydraulic sheet bending press must be additionally equipped with a flattening tool. This upgrade makes it possible to reduce the bending angle to less than 24 degrees. Sheet metal with a thickness of 0.1 to 1.5 mm can be flattened.
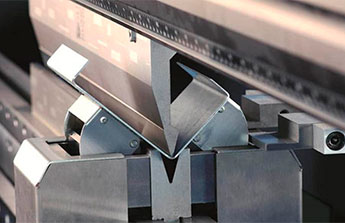
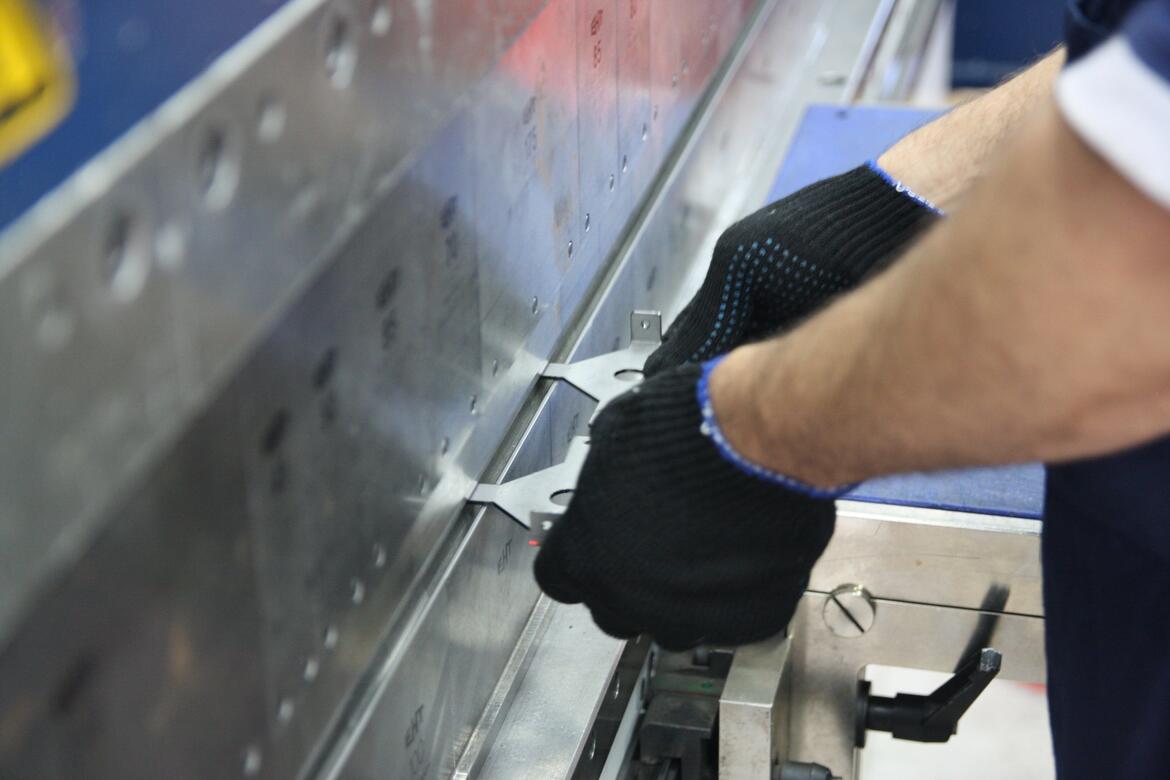
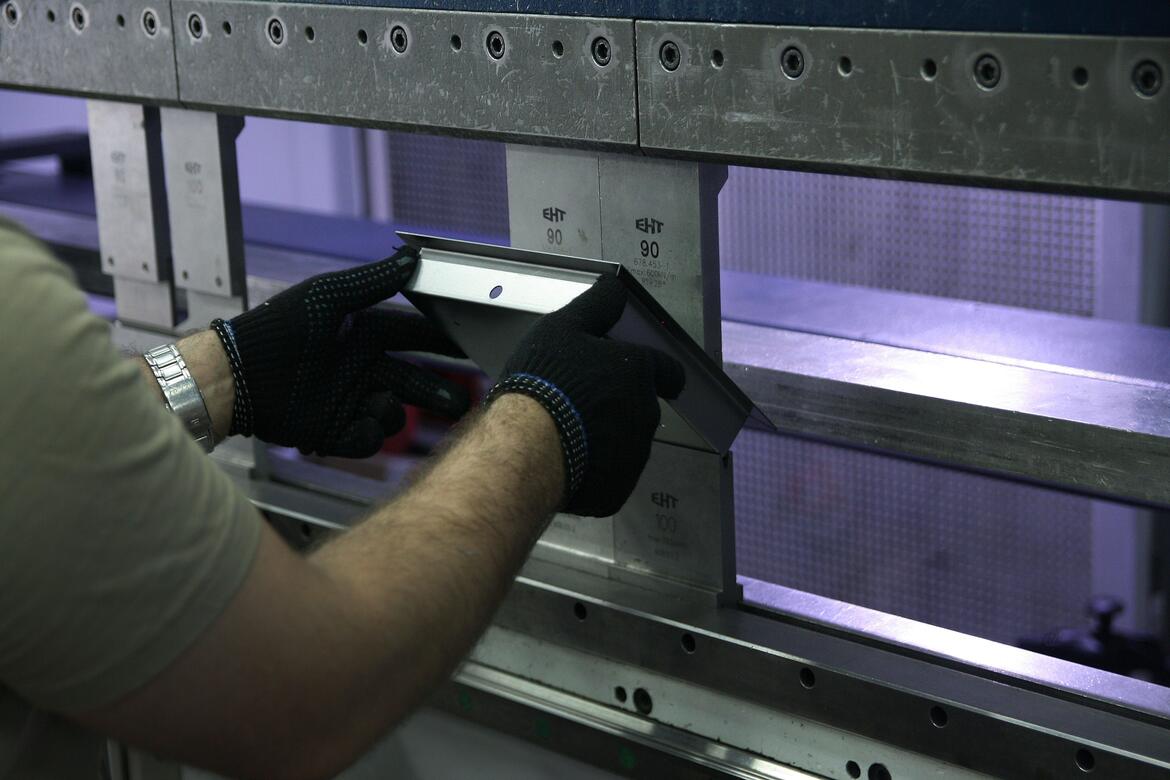
Technologically, the bending process takes place in several stages:
The workpiece is successively exposed to several types of influence:
- Elastic tension
- neutral position
- Plastic tension
As a result, a high-quality, high-precision part is invariably obtained, which is completely ready for further stages of production of the final product (welding, assembly, installation of welded and zeroed fasteners, powder coating, etc.).
This method of sheet metal processing is widely used in:
- Mechanical engineering, production of parts for aircraft and automobile construction, agricultural machinery
- Production of chemical, medical and food equipment.
- Production of trade equipment, household appliances, souvenir products, etc.
- Production of metal furniture, architectural elements, quick-mounted and general construction structures
- Production of advertising structures, fastenings.
- Production of tools and technological equipment
Advantages of metal bending technology:
- There is no need for careful preliminary preparation of the metal surface.
- Bending replaces unnecessary welds, which improves the appearance of the product and reduces the need for post-processing.
- The metal in the bending zone completely preserves its physical, mechanical and chemical properties.
- Due to the absence of thermal impact on the metal provided by the sheet bending machine, the manufactured parts have high strength and durability.
- High speed of production of parts. The required results and shape are achieved quickly, in one bending cycle.
- Bending of metal ensures complete tightness of the final product, correctly made bends are not prone to corrosion.
- Thanks to the use of CNC presses, bent parts fully meet the requirements of technical specifications and drawings. Excellent stability and repeatability of results is ensured.
- This sheet metal processing technology does not require the use of process gases, fillers and other consumables.
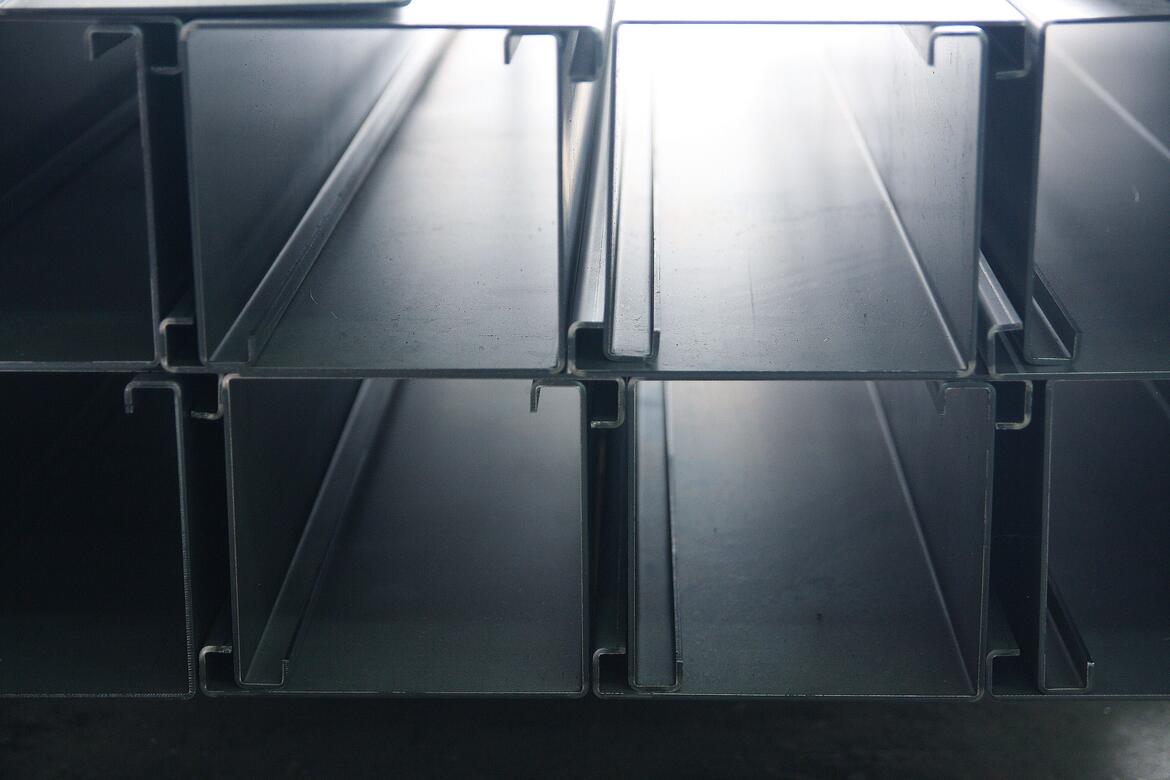
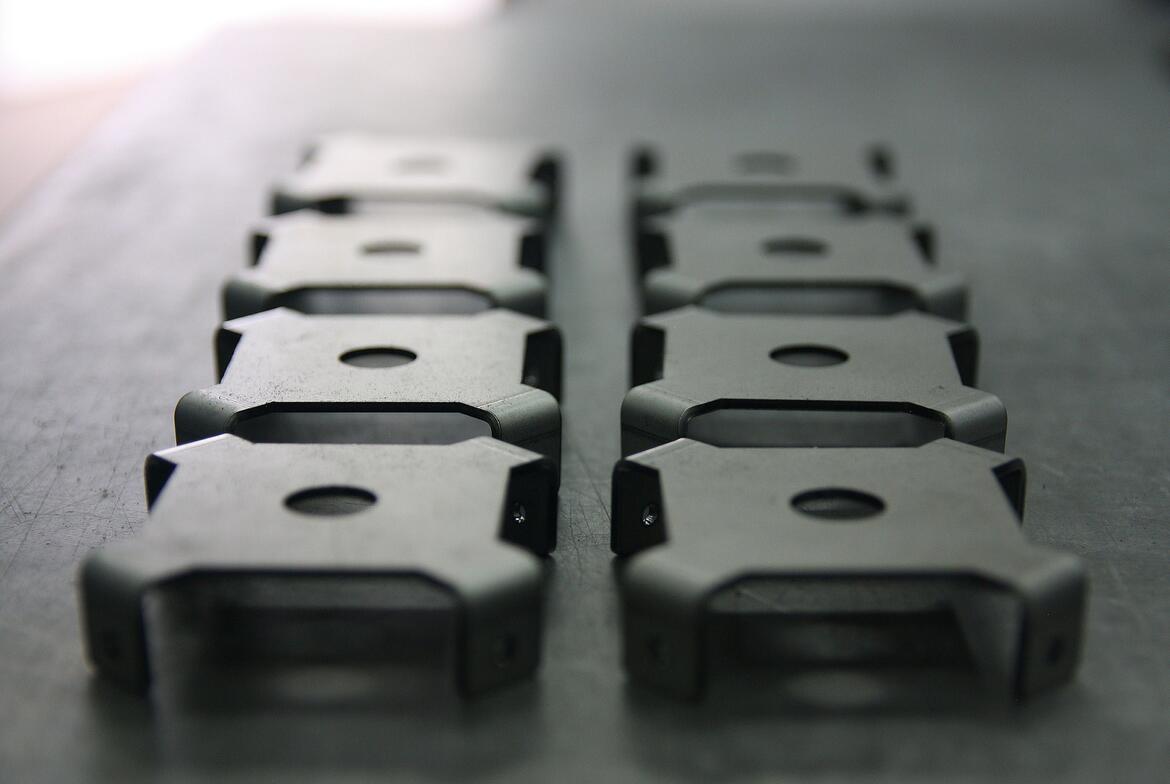
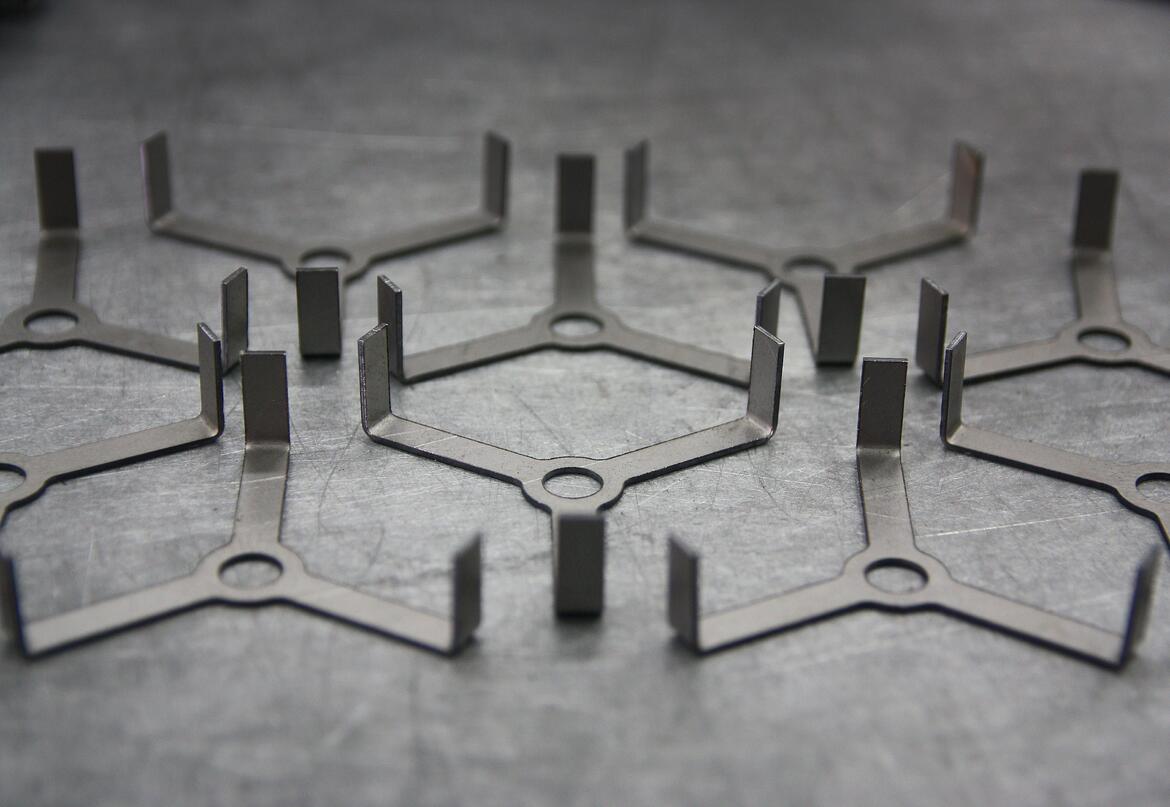
Factors affecting the quality of metal processing by cold bending technology :
The thickness of the workpiece. For the processing of thick slabs (blanks), more effort is required from the hydraulic sheet-bending press. When processing thick plates, the process of lowering the working beam of the machine slows down, the working time of the tool increases (the bending speed decreases), and the total operation time increases.
The total length of the bend during the plastic deformation service. This factor determines the number and composition of working tools used on a hydraulic press brake. With an increase in the length of the bend, the labor-intensiveness of positioning the workpiece in the working area of the hydraulic sheet-bending press significantly increases, the wear of working tools is noticeably accelerated, which inevitably entails an increase in the cost of the service.
Total weight of the part (workpiece) . This important factor affects the duration of preparatory operations, the labor-intensiveness of positioning the workpiece in the working area of the hydraulic sheet-bending press, complicates intra-production logistics, and increases the total time of metalworking.