Laser Metal Cutting
The company LLC Production Complex "Svet Shakhtyora" offers laser cutting services on professional laser cutting complexes with ARAMIS thermozones, which allow for high precision and cutting quality with minimal waste of metal 0.5-14.0 mm thick with a processing range of 3000 × 1500 mm, and also with the possibility of cutting galvanized and non-ferrous metals up to 6 mm.
Laser cutting of sheet metal is an advanced technology for processing (cutting) various types of materials, widely used all over the world. Speed, flexibility, accuracy, high quality and low cost - this is not a complete list of the main advantages of this technology. Thermal heating of the required section of the metal sheet for the formation of the melt zone and, partially, evaporation is carried out by exposing it to a narrowly directed laser beam of high power and coherence.
Further removal of molten metal from the cutting area takes place under the influence of process gas supplied to the cutting zone under high pressure. There is also a partial evaporation of metal from the processing area. As a result, laser cutting of sheet metal is geometrically precise and consistently high-quality. There is practically no taper, scale, breakage, burrs.
An almost perfectly smooth cut edge is formed, which does not require additional processing and has no traces of geometric defects. The resulting parts are fully suitable for any further production operations of the final product.
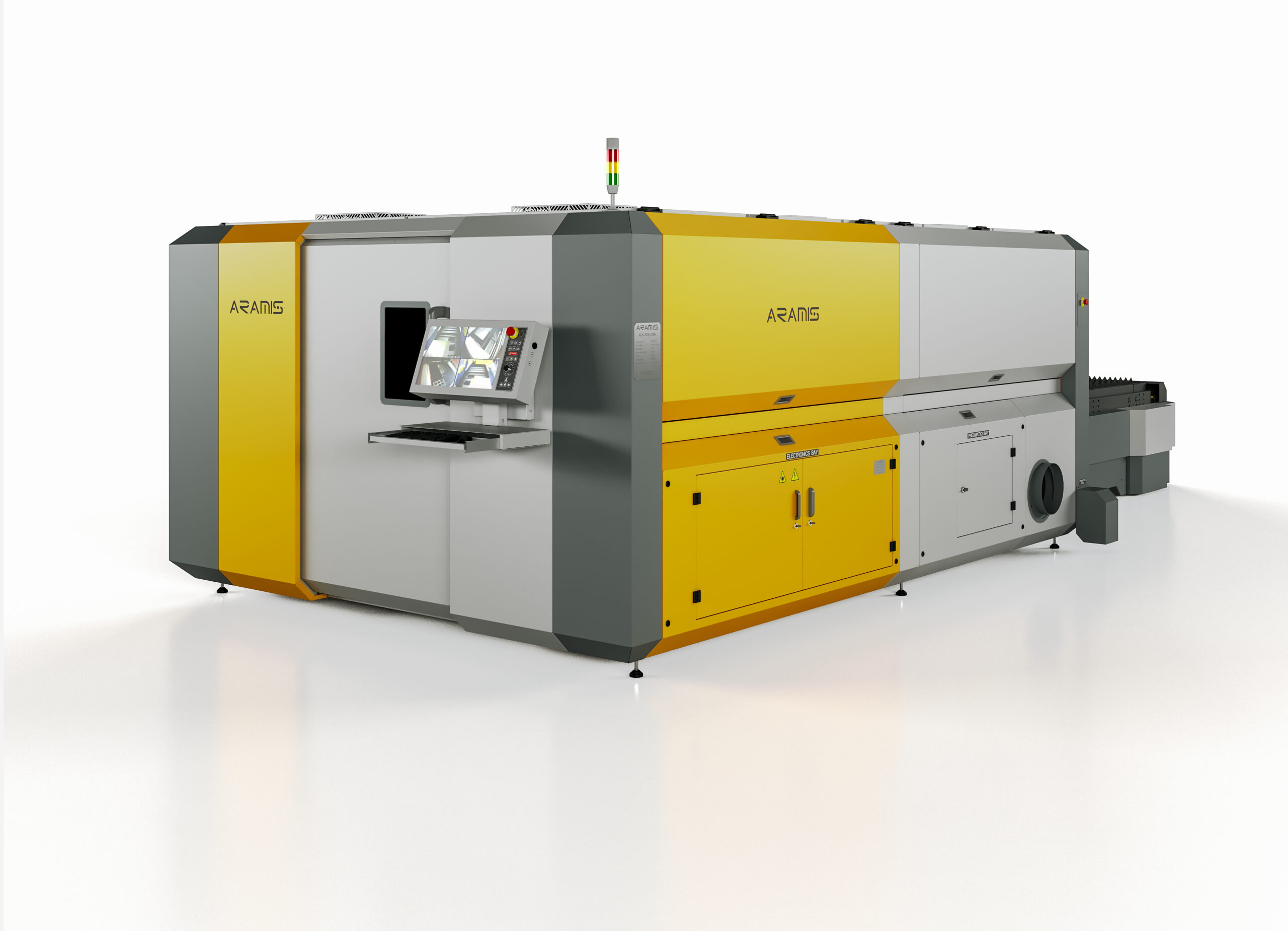
Today, this method of processing sheet material is used in:
- Mechanical engineering, production of parts for aircraft and automobile construction, agricultural machinery
- Production of chemical, medical and food equipment.
- Production of trade equipment, household appliances, souvenir products, etc.
- Production of metal furniture, architectural elements, quick-mounted and general construction structures
- Production of advertising structures, fastenings.
- Production of tools and technological equipment
Factors affecting the quality of laser metal cutting:
In order to achieve the necessary results during laser metal processing, it is necessary to carefully approach the selection of cutting equipment, processing parameters, as well as the process gas that will be used to cut the metal. Dozens of settings of the cutting complex directly affect the quality and speed of manufacturing parts.
It is necessary to take into account the operational characteristics and capabilities of the equipment used, the overall dimensions of the manufactured part, requirements for geometric accuracy and cut quality, the type of processed alloy and the thickness of the processed part.
It is important to understand that laser metal cutting is usually only the first step in the manufacturing process of the final product. Therefore, it is necessary to take into account what technological operations the processed part will undergo at the next stages of production.
As for the speed that laser metal cutting can provide, it is ultimately affected by the thickness of the workpiece and the type of alloy, the level of thermal conductivity and the degree of reflection of the metal, the power and technical capabilities of the laser equipment used, etc.
Advantages of technology:
- In the process of laser processing (cutting), metal particles are melted under the influence of high-power coherent, narrowly directed and focused laser radiation, partially vaporized, and also blown out by a stream of process gas, which is fed into the laser processing zone under high pressure. As a result, narrow, high-precision and clean metal cutting results are obtained with a relatively small heating zone. Relatively low thermal impact on the workpiece and manufactured products. The part avoids changing the geometry and distortion of the product.
- During laser processing of metals, there is no mechanical effect on the processed material. This avoids changing its structure. Also, the original texture of its surface is completely preserved, which can be important in the manufacture of decorative and architectural elements without further application of decorative coatings.
- Correct selection of cutting modes and careful processing of sensitive metals can avoid thermal deformation of parts.
- CNC laser cutting systems allow you to cut thick and thin rolled metal at high speed. The linear drives of the portal coordinate systems of our machines provide the highest speeds (synchronous up to 150 m/min) and acceleration (up to 2g) of the movement of the cutting optical head. The speed of metal cutting can be significantly increased due to the correct selection of cutting modes and pressure of process gases.
- Thanks to the optimization of the placement of the blanks, waste is reduced to a minimum. This is especially important when machining expensive materials and alloys.
- Cutting of sheet metal ensures a significant reduction in the cost of small and medium-scale production of metal products. Because there is no need to make molds, stamping tools, casting molds with alternative methods of production of finished products.
- Metal cutting using CNC and high-precision portal coordinate systems allows you to ensure geometric cutting accuracy with minimal errors (no more than 0.05 mm). The technological capabilities of our equipment allow us to perform complex metal processing with tolerances of the 14th quality.
- The technology makes it possible to mark and mark manufactured parts using technological (including raster) engraving.
- In the process of laser cutting, with a qualified selection of cutting modes, scale, burrs and other critical cutting defects are not formed. The manufactured parts are ready for further stages of production without additional processing.
- Metal cutting guarantees perfect repeatability of the resulting products, which is especially important for large-scale serial and serial production.
- It is possible to cut a wide variety of metals, regardless of their thermophysical, chemical, optical properties: galvanized steel, carbon steel, stainless steel, alloy steel, heat-resistant steel, structural steel, armor steel, aluminum, aluminum-based alloys, copper, copper-based alloys ( brass, bronze), titanium, titanium-based alloys, etc.